In the early 2010s, the process of additive manufacturing was beginning to really take off. While not a new technology by any means (the concept had already been around for decades), the seemingly limitless possibilities of 3D printing had grabbed hold of manufacturers, the mainstream media, and hobbyists alike.
“It’s the wave of the future,” they claimed.
Little did they know that this future they were heralding would rest squarely on the shoulders of jet milling and air classification.
The importance of quality materials in additive manufacturing
Typically, there are three things required for an additively manufactured object:
1 . A highly advanced 3D printing machine
2 . A 3D model created using a computer-aided design (CAD) package
3 . The right material for the job
It’s this last piece that has proven most difficult for many industries in recent years. While modern advancements have allowed for the use of some metals and ceramics, traditionally additive manufacturing was done using specialized polymers, due to their pliability and ease of manufacturing.
In a process where each layer is effectively fused on top of the last, selecting the right material is crucial for success. A polymer with too many imperfections or too broad of a size distribution can lead to product defects and a compromised structural integrity. In an industry such as aerospace engineering for example, this is something that is simply unacceptable.
Pounding out the ideal particle size
A customer came to AVEKA recently with a challenge they were facing. They were attempting to additively manufacture a product using a particular polymer – an engineered thermoplastic – but were running into difficulties getting the consistent results they needed. The problem was believed to be due to particle size distribution of the polymer powder used in the 3D printer, so the customer was looking for a more effective way to mill the polymer to the desired particle size. These thermoplastics are difficult to mill due to their mechanical properties which make them very tough.
Jet milling was the ideal choice for milling our customer’s polymer, since it uses room-temperature air and introduces no significant heat sources throughout the process. Heating up thermoplastics only makes them softer and more pliable when we instead need them to stay cool and friable in order to be easily broken down to the required size. Further, jet milling has the high energy input necessary for rapid milling of these tough polymer particles.
After initial jet milling tests, it was then determined that there were too many fine particles in the jet milled powder which were contributing to the difficulty in 3D output consistency. To solve these issues, the team determined that a combination of jet milling and air classification would be required.
Jet milling and air classification – a two-pronged attack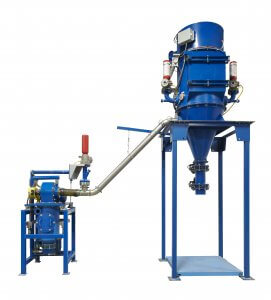
In order to solve our client’s problem, a two-step process needed to be implemented:
1 . First, the particles were put through the jet milling process to break them down to near the target size.
2 . Second, all particles finer than the allowable limit were removed through the air classification process.
Jet milling, in the simplest terms, is the process by which particles are accelerated via high velocity air streams, powered in this case by a turbulent 3-jet system. Confined inside the machine, the particles collide into one another, causing breakage and improved separation. The integral classifier within the jet mill controls the size that particles must reach before they can leave the mill. Those that are small enough exit the mill as jet milled product, and those that are too large are sent back to the mill bed for further size reduction.
After jet milling, the reduced particles are transferred to a separate secondary centrifugal air classifier. By adjusting the rotor speed, feed rate, and air flow of the air classifier, we are able to separate out the particles that fall within the target range and remove the undesirable fine particles.
Trials and (overcoming) tribulations
Now that we had a proposed process in place, the next step was to thoroughly test it. Using small pilot batches, AVEKA was able to successfully jet mill and air classify the particles to the client’s desired particle size range. Using our particle size analyzer, we were also able to verify that all particles finer than the allowable limit were removed from the final output.
With successful trial and pilot runs in place, we were then able to quickly ramp up to full-scale production. The customer was able to additively manufacture their product with much greater success and were so pleased with the engineered polymer that we continue to manufacture it for them to this day.
Create your ideal materials with AVEKA
With over 25 years of experience, we know what it takes to process your materials, custom for your unique needs. Whether that involves jet milling, air classification, or over a dozen other specialty services, we have the equipment and the expertise necessary to take your product from a 3D model to a 3D masterpiece. Contact us today for an initial feasibility assessment.